Ferroalloy, in a broad sense, refers to a product that is added to molten iron as a deoxidizer, element additive, etc. during steelmaking to give the steel certain characteristics or meet certain requirements. The intermediate alloy composed of iron and one or more elements is mainly used in steel smelting. In addition, alloying will also change the mechanical properties of the parent material, producing hardness, toughness, ductility, etc.
Different Types Of Ferro Alloy
The main products of ferroalloys are ferroaluminum, ferrosilicon, ferronickel, ferromolybdenum, ferrotungsten, ferrovanadium, ferromanganese, etc. The production of a specific ferroalloy involves many processes that must be followed to obtain the desired physical and mechanical properties. Slight differences in temperature, heating or composition can produce alloys with completely different properties.
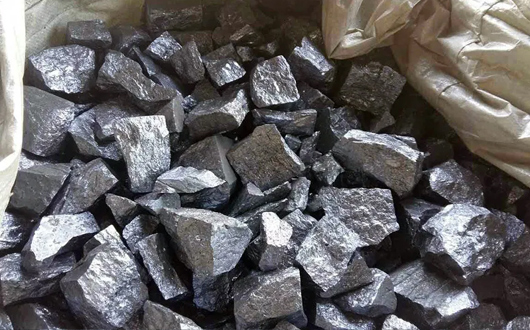
Ferroalloy Products
Ferromolybdenum
Ferromolybdenum is often used in the production of alloy steel to improve the hardness, toughness and wear resistance of steel. The molybdenum content in ferromolybdenum is generally between 50% and 90%, and different uses require different contents of ferromolybdenum.
Ferrosilicon
Ferrosilicon generally contains 15% to 90% silicon, with a high silicon content. Ferrosilicon is an important alloy material, and its main application is steel production. Ferroalloys help deoxidize steel and ferrous metals. In addition, it also improves hardness, strength and corrosion resistance. China is the main producer of ferrosilicon.
Ferrovanadium
Ferrovanadium is generally used to produce alloy steel to improve the strength, hardness and wear resistance of steel. The vanadium content in ferrovanadium is generally between 30% and 80%, and different uses require different contents of ferrovanadium.
Ferrochrome
Ferrochrome, also known as chromium iron, is generally composed of 50% to 70% chromium by weight. Basically, it is an alloy of chromium and iron. Ferrochrome is mainly used to produce steel, accounting for about 80% of the world's consumption.
Generally speaking, ferrochrome is produced in electric arc furnaces. The production process is essentially a carbothermic reaction, which takes place at extreme temperatures approaching 2800°C. A large amount of electricity is required to reach these high temperatures. Therefore, it is very expensive to produce in countries with high electricity costs. The main producers of ferrochrome are China, South Africa and Kazakhstan.
Ferrotungsten
Ferrotungsten is commonly used in the production of alloy steel to increase the hardness, wear resistance and high temperature resistance of the steel. The tungsten content in ferrotungsten is generally between 60% and 98%, and different applications require different contents of ferrotungsten.
The production of ferrotungsten is mainly carried out by blast furnace ironmaking or electric furnace method. In blast furnace ironmaking, tungsten-containing ore is placed in a blast furnace together with coke and limestone for smelting to produce ferroalloys containing tungsten. In the electric furnace method, an electric arc furnace is used to heat and melt the raw materials containing tungsten to prepare ferrotungsten.
Ferrotitanium
The titanium content in ferrotungsten is generally between 10% and 45%. The production of ferrotungsten is mainly carried out by blast furnace ironmaking or electric furnace method. China is one of the largest producers of ferrotungsten in the world.
Uses Of Ferroalloys
The main uses of ferroalloys are civil construction, decoration, automobiles, steel industry and electronic equipment. The steel industry is the largest consumer of ferroalloys because ferroalloys impart various properties to steel alloys and stainless steel.
Alloy steel production
Ferroalloys are one of the important raw materials for making alloy steel. By adding different kinds of ferroalloys (such as ferrochrome, ferromanganese, ferromolybdenum, ferrosilicon, etc.) to steel, the properties of steel can be improved, such as improving hardness, strength, wear resistance, corrosion resistance, etc., making steel more suitable for different engineering and manufacturing fields.
Cast iron production
Cast iron is a common casting material, and ferroalloys play an important role in cast iron production. Adding a certain proportion of ferroalloys can improve the mechanical properties, wear resistance and corrosion resistance of cast iron, making it more suitable for the manufacture of mechanical parts, automotive parts, pipelines, etc.
Power industry
Ferroalloys are also used in the power industry, such as as core materials for power transformers. Alloy iron has good magnetic permeability and low hysteresis, which can effectively reduce the energy loss of power transformers.
Aerospace field
The application of ferroalloys in the aerospace field is also very important, such as for the manufacture of structural parts and engine parts of aircraft and rockets, which require these parts to have characteristics such as lightweight, high strength and high temperature resistance.
Chemical Industry
In the chemical industry, ferroalloys are often used as catalyst carriers in organic synthesis reactions, gas purification and other processes.
Refractory materials
Certain ferroalloys can also be used in the preparation of refractory materials to improve the high temperature resistance of the materials. They are often used in the manufacture of refractory materials in industries such as ironmaking and steelmaking.